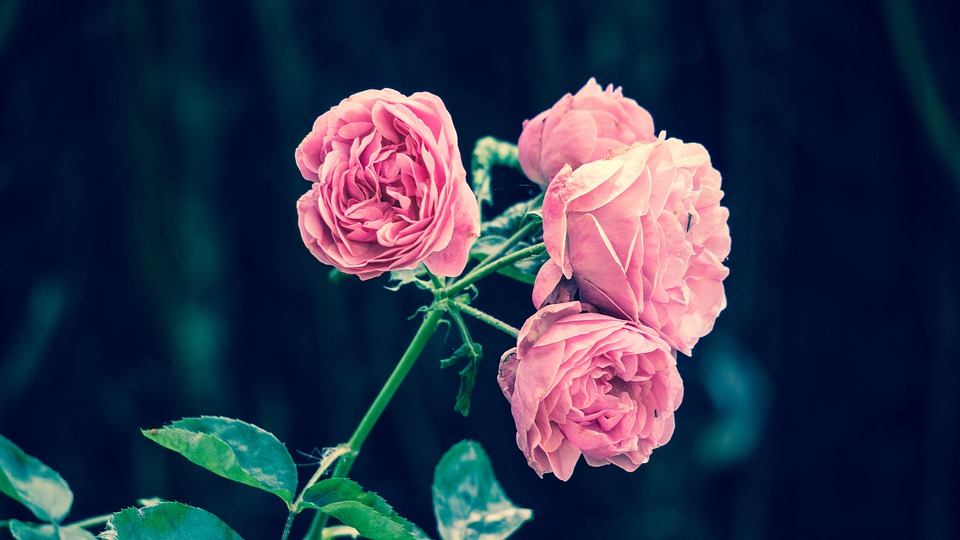
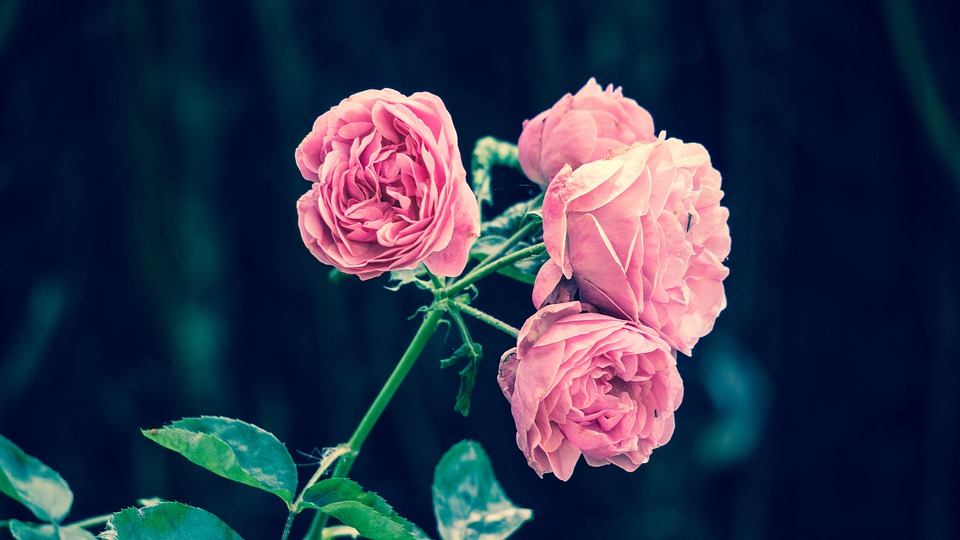
Rose essential oil has been used by people all around the world for different purposes for many centuries. Even when it was available mostly for the posh community of people, its charm was always alluring for the common man.
In the modern world, the rose essential oil might be expensive but it is still within the reach of common man. Ever thought about the process of how rose essential oil is prepared from the delicate petals of rose flower? Here we will discuss two processes- distillation and extractions which are used to make the best quality rose essential oils.
Picking of Flowers: Flowering in rose plantation commences two years after planting. However, the full flower production can be expected in third year onward. The flowers are picked daily early in morning so as to complete the operation before the sunrise. Depending upon the soil and management practices flower yield in sub-tropical climate from third year onward ranges form 2000-3000 kg/ha/year.
In temperate climate flower yield ranges form 4000-5000 kg/ha/year. Flowering in sub- tropical climate starts from middle of March and ends up by 3rd week of April. In temperate climates, blossom starts in May and continues for about 50 days.
Rose Oil Distillation Process:
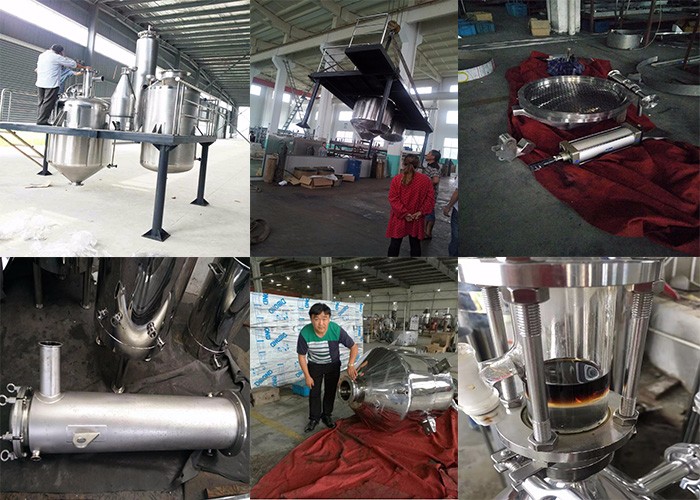
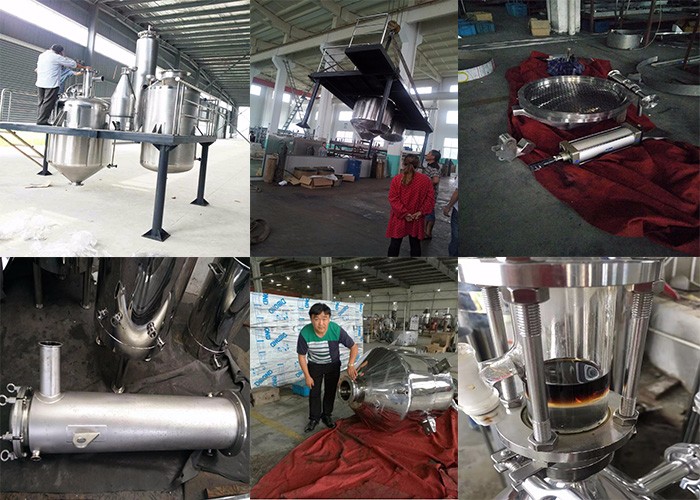
As soon as the harvesting is over flowers are taken to distillation plant for processing. In case, there is delay in processing, flowers should be spread in shade at low temperature and water should be sprinkled to avoid the loss of oil through evaporation.
In India, three different methods are in practiced for the processing of rose oil.
1. Deg and Bhapka Method:
Majority of rose distillers in India use traditional distillation equipment which consists of round kettle (deg) and a receiver (bhapka), which also serve the purpose of condenser. These are made of copper. The kettle and the receiver are connected with bamboo (chonga) through which steam from kettle reaches to the receiver.
The receiver is placed in a small water tank which helps in the condensation of vapours containing rose oil.
The kettle has a capacity of 50-100 kg. flowers per batch and takes about 6-8 hours to complete the distillation. After distillation is over the receiver is removed and oil is separated. This method gives a recovery of 0.01-0.015% which is significantly lower than the other methods described below.
2. Direct Fired Distillation Unit: The unit consists of a kettle (still), a column, condenser and receiver The Whole unit can be of copper or stainless steel. The capacity of still may range form 250 kg. flowers per batch. To increase the fuel efficiency and to generate sufficient steam, fume tubes are fitted in the bottom of the still. The outlet of the receiver is connected with the column to recycle the condensate into the still, after the separation of oil takes place in the receiver. This process in known as Cohobation” which has been found to improve the recovery; of oil. The plant is simple in operation and can be operated by a semi-skilled worker Direct fired plant may cost Rs. 1.25-1.5 lakh, if made out of stainless steel. The plant takes about 4-6 hrs per batch for completion of distillation.
3. Boiler Operated Unit: This is most modern method of distillation and suitable for large-scale production of oil. The whole plant consists of three units, a boiler, a distillation unit and a “Cohobation” unit.
Flowers are charged in the distillation unit and distillate after passing through a receiver fed to another still through cohobation column to ensure complete recovery of oil. Part of the oil is also collected from the first receiver and the remaining from the second. It is advantageous to collect the distillate from the second separator and feed back it to the distillation tank in pace of fresh water.
Complete distillation in boiler operated distillation unit takes 4-5 hrs. The oil recovery varies from 0.025% -0.03%. Depending upon the capacity ;of the boiler, the unit may cost Rs 6-8 lacs. The other advantage with the system is that several distillation units can be connected with the boiler.
Oil content and Yield: Although scattered flowering may be noticed in the planting year itself, optimum flower yield is obtained in third and subsequent years of plantation. This yield level is maintained until ten years of plantation, thereafter tends to decline. In subtropical climate an average flower yield of 200-300 kg in the first year, SOO- 800 kg in the second year and 200-300 kg. /ha.
In third and subsequent years of planting is obtained. Thus. with an average 0.020% recovery, oil yield during third and subsequent years may vary from 0.4 to 0.60 kg/ha/year. Considering an average recovery of 0.03% oil in temperate climate, the oil yield in third and subsequent year may range from 1.20 kg to 1.50 kg/ha/year form 4000 to 5000 kg flowers/ha harvested each year.
Every Method has Its Own Pros & Cons
No doubt that there are different pros and cons of the different processes of the extraction and the distillation but this article explains the major ways in which the rose oil is distilled and extracted.
There are some other ways that are used for the extraction of the rose essential oil but they are not so commonly used and some of them are specific to the country where they are used. Above given are the methods that are followed worldwide by the distillers & manufacturers to produce rose essential oils.